Ausführung Phase I
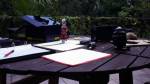 |
Dem eigentlichen Bau gingen verschiedene Stufen der Planung voraus. Die Ideen zu diesem Rad gingen mir schon viele Jahe durch den Kopf und ich hatte es sehr oft auf Papier gebracht, so daß ich das Grundprinzip auch schon fertig entwickelt hatte. Während der Bauphase kam es darauf an, die Details ausführbar zu gestalten.
|
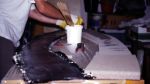 |
Der Hauptrahmen besteht aus 3 jeweils 15mm starken Platten aus PVC-Schaum mit einer Dichte von 80 kg/m³. Die Platten wurden mit Epoxidharz und einer Lage 80-Gramm-Kohlefaser Köper miteinander verklebt. Zuvor wurden die Platten mit einer angedickten Epoximischung eingestrichen, um ein zu starkes Eindringen des Epoxidharzes in den Schaum zu verhindern.
|
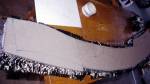 |
Nach dem Aushärten des Harzes wurden auf die verklebten Schaumplatten die Konturen des Rahmens aufgetragen.
Anschließend wurde der Rahmen per Stichsäge grob ausgeschnitten und verschliffen. |
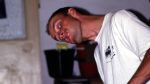 |
Wichtig:Epoxidharz ist für den menschlichen Körper nicht ungefährlich. Wenigstens eine minimale Schutzausrüstung sollte getragen werden, dazu sollte der Raum gut belüftet sein und jeder Körperkontakt mit dem Harz vermieden werden. Es gibt gute Cremes, die die Haut kurzfristig schützen, ansonsten sollten Handschuhe der CE-Schutzkategorie III benutzt werden. |
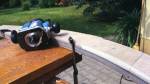 |
Nach dem Schleifen des Rahmens und Ausarbeiten der Öffnungen wurden die Kanten mit einer Oberfräse gerundet. Anschließend wurde per Hand mit Schleifpapier nachgearbeitet. Der Schleifstaub von Kohlefaser ist für die Maschinen und auch den Menschen gefährlich, da er elektrisch leitend ist und in die Atemwege eindringen kann. |
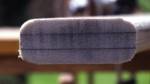 |
Das Bild zeigt den Zwischenschritt zwischen dem Fräsen und dem anschließenden Schleifen.
Gut zu erkennen die Zwischenlagen aus Kohlefaser. Sie versteifen den Rahmen zusätzlich, sind aber vor allem entstanden, da wir den 15mm-Schaum noch für andere Projekte brauchten. Das Mehrgewicht durch die Zwischenlagen beträgt ca. 300 Gramm, der Schaumkern wiegt damit insgesamt ca. 950 Gramm. |
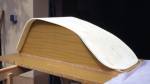 |
Die erste Idee für den Sitz war eine Schale zu kaufen und diese dann einfach auf den Rahmen zu montieren, nach kurzen Diskussionen entschieden wir uns aber doch, den Sitz komplett selber zu bauen.
Die Form entwickelten wir Stück für Stück über Sitzversuche und kleine Nacharbeiten, ehe wir die Form fürs Laminieren fertigten. |
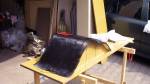 |
Laminiert wurde mit 80 Gramm Köper im Vakuumverfahren, die Rückseite einlagig, Vorderseite im Anschluß daran zweilagig.
Nach dem Aushärten wird der Sitz beschnitten und auf dem Rahmen fixiert. Die endgültige Bearbeitung erfolgt erst nach Fertigstellung des Hecks. |
Phase I wurde im Januar 2003 beendet und es folgten erste Testfahrten. Allerdings erwies es sich als großer Nachteil, daß kein Gepäcktransport möglich war, ebenso das Tragen eines Rucksackes. Deshalb habe ich mich auf einige wenige Touren in der Umgebung beschränkt. Einmal fuhr ich auch mit dem Anhänger von Axel eine Runde.
Als problematisch erwies sich schon zu dem Zeitpunkt die Lenkstange, hier mußte ich auf jeden Fall sofort etwas umbauen... und dabei blieb es den gesamten Sommer hindurch.
Statt dessen baute ich einen Hänger, segelte etwas und nutzte den Hänger für eine Biketour (Tandem) durch Ungarn.
Bei den wenigen Testfahrten zeigte sich auch noch ein anderes Problem. Der Dreck fliegt direkt in den Nacken, was zur
Ausführung Phase Ia
führte:
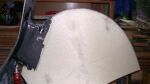 |
Als Vorgriff auf den Anbau des Hecks baute ich einen Kotflügel.
Den Kotflügel mußte ich zweimal bauen, der erste Entwurf passte nicht richtig über die einfedernde Schwinge, sondern schliff an den Seitenwänden.
Dieses Problem versuchte ich zuerst durch aufbiegen und aussteifen zu beheben. Beschloß dann aber doch, das Teil noch einmal neu zu bauen.
Die Ausführung erfolgte ähnlich wie bei dem Hänger und auch als Vorgriff auf den Bau des Kofferraumes in Sandwitch-Bauweise. Um den Preis niedrig zu halten und auch, weil eine gewisse Materialstärke notwendig ist, verwendete ich hier jedoch Glasfaser mit 160 g/m² als Trägergewebe.
|
Ausführung Phase II
In Phase II war Hauptziel der Anbau des Gepäckraumes, daneben mußte ich auch das Problem der Lenkung lösen und die Umlenkrolle brauchte eine Abstützung:
Für den Bau des Hecks versuchte ich die Bauweise des Hängers zu adaptieren und wollte dadurch den komplizierten Formenbau einsparen. Ich verwendete die gleichen 5mm starken Schaumstoffplatten, mit denen ich auch den satellite baute. Die Platten sind nur etwas formbar, so daß insgesamt eher flächige Teile zusammengesetzt werden mußten.
Später sah ich im Internet, daß andere vergleichbares probierten, indem sie Isomatten als Sandwitchmaterial verwendeten. Isomatte ist in meinen Augen als Sandwitchkern allerdings nicht so geeignet, da sie im Verhältnis zum Gewicht doch relativ weich ist. Dies erfordert einen stärkeren Materialaufbau. Von Vorteil ist sicherlich die leichte Verformbarkeit.
Die einzelnen Bauphasen jetzt in der Übersicht:
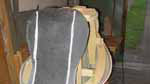 |
Als erstes entsteht ein Spantengerüst aus Haupt und Nebenspanten, die die Form vorgeben und gleichzeitig stabilisierend während der einzelnen Laminierschritte wirken.
Das Spantengerüst wurde so gefertigt, daß es nach Schließen der Form problemlos demontiert werden kann.
|
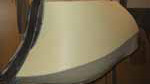 |
An das Spantengerüst werden anschließend die einzelen Platten angeformt und fixiert. Schwierigkeiten ergaben sich hierbei auf Grund der relativen Steifigkeit des Sandwitch-Schaumes.
|
 |
Die Kanten werden gesondert wurch eine Lage 180er Biaxial Kohlegelege versteift, anschließend wird die gesamte Außenfläche mit 160er Glasgewebe überzogen.
Auch hier verwendete ich "nur" Glasgewebe. Durch den Einsatz von leichterem Kohlegewebe (oder auch leichterem Glasgewebe), hätte sicherlich Gewicht eingespart werden können. Jedoch hatte ich Bedenken wegen der Druckempfindlichkeit.
|
 |
Erste Sitzproben auf dem halbfertigen Bike.
|
 |
Ein grosser Nachteil des Baus als Sandwitch ohne Negativform ist die aufwendige Nacharbeit an der Oberfläche. Mehrfaches Spachteln / Schleifen / Spachteln ... war die Folge.
|
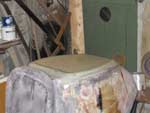 |
Anformen des Deckels.
Der Deckel entstand mit dem selben Schaum als Kernmaterial wie das gesamte Heck. Als Verstärkung für die Kanten verwendete ich mehrere Lagen Biaxial-Glasgewebe.
|
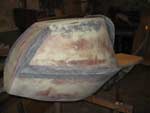 |
Ein weiteres Bild vom geschliffenen und gespachtelten Heck.
|
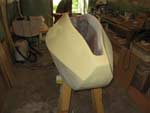 |
Letzte Phase - Feinfinish.
Hierzu verwendete ich Füller aus dem Autobedarf. Auch hier galt es wieder mehrfach aufzutragen und mehrfach zu schleifen.
|
Ausführung Phase III
Phase III beschreibt die ersten Testfahrten und den resultierenden Änderungsbedarf.
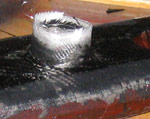 |
Bei den ersten Testfahrten ergab sich, daß das Tretlager viel zu dicht am Sitz positioniert ist. Ursprünglich war geplant, ein verschiebbares Lager einzubauen, was jedoch auf Grund der doch eher komplizierten Konstruktion gestrichen wurde.
Statt dessen bin ich davon ausgegangen, daß ich im Notfall einfach ein neues weiter vorne einbauen könnte.
|
|
|
Weiter zu den Bildern
Technische Daten
(Zustand 09/2004)
|
Länge: 2,70 Meter
Achsstand: 2,10 Meter
Sitzhöhe über Boden: 37 Zentimeter
Gewicht (aktueller Zustand): 19,50 Kilogramm
|
|